DTF printers have been popular around the world in recent years, and major clothing printing manufacturers are investing in production. Now that the northern hemisphere is in summer mode, T-shirts are an indispensable necessity for both men and women, young and old. However, when talking with DTF manufacturers, I found that some customers do not pay attention to some problems in the use process, which will lead to poor DTF printing effect, such as the residue of hot melt powder, which will make customers doubt whether it is the problem of the machine they bought.
First of all, we have to admit that there may be a problem that the machine is not easy to use, and secondly, in response to this problem, the manufacturers have given the following answers.
First of all, we need to briefly explain the printing process of the DTF printer. At present, the ordinary DTF printers on the market are basically designed by computers first, and then printed by computer instructions. The design pattern is printed on a PET film. Then the hot melt powder evenly spread on the hot stamping pattern, and then the excess hot melt powder shake off, and finally the hot stamping pattern with good hot melt powder is dried.
The printing steps of the DTF printer are very simple, and if there is a problem with the materials and time used during the period, as well as temperature and humidity control, there may be a phenomenon of unclean shake powder.
1. Ink problem
During the printing process, if the concentration of white ink is too low, it is very thin, and there is too much water, it is easy to appear ink flow (the oil and water of white ink permeates outside the edge of the pattern), which leads to too much hot melt powder sticking on the edge of the pattern when shaking the powder. It can be observed that if there is water stain around the printed film pattern before using hot melt powder, it can be determined that the ink is the problem.
Solution: Changing the ink or pre-drying it before dusting can improve the condition.
2. Hot film quality problem
If in the same consumables under the same production environment, after changing another hot stamping film, the sticky powder problem is improved, then there is a high probability that the hot stamping film quality is poor, unqualified, or the hot stamping film and ink compatibility is not good enough.
Solution: Replacing the appropriate hot film can solve this problem.
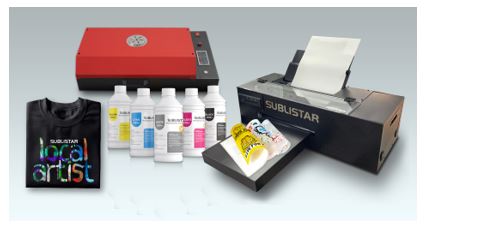
3. Hot melt powder problem
If the hot melt powder is damp, it will stick to powder and become Tuo, and the pattern edge will also appear obvious glue edge.
Solution: The hot melt powder needs to be treated with moisture, or the powder that has been damp is slightly baked and then sifted into the powder shaking machine. Sublistar brand powder shaker is recommended here. Because its powder silo has the function of preheating, it can effectively solve the phenomenon of hot melt powder caking and moisture. The smooth coating inside the powder silo is to ensure that the hot melt powder can flow smoothly after preheating and drying, so as to ensure smooth printing and avoid the phenomenon of rubber edges caused by moisture.
4. Humidity problem
Due to the weather, the air humidity is too large, it will cause the white ink to dry slowly, and the wet white ink will make the edge of the pattern adhere to too much hot melt powder, forming powder edge and glue edge.
The solution is to choose a printer and a powder shaking machine with a pre-drying system. If the DTF printer contains a temperature and humidity controller, it is best to choose this configuration and adjust the indoor air conditioning temperature and humidity according to the temperature and humidity situation in time. If there is no indoor air conditioning, there is a temperature and humidity reminder, then you need to adjust the production demand in a more timely manner to avoid excessive humidity, which affects the overall printing.
Note: When the air humidity is too high (above 65%), it needs to be dehumidified to protect the machine.
If the machine is not grounded, the static electricity of the hot film is large when the weather is dry, and the problem of sticking powder is easy to occur, and the ground wire can be improved by connecting the machine.
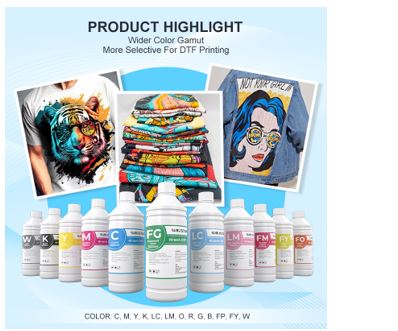
5. Machine problems
If the above factors are excluded, there is still dirty hot melt powder on the hot stamping film, it may be the quality of the DTF printer itself is not up to standard.
After the Sublistar printer prints, it’s time for the powder shaker machine. First in the powder bin for preheating, and then for circulating vibration powder, and then the release of flapping powder, then into the oven, automatic conveyor belt, tunnel drying, drying after the automatic winding system.
And sublistar’s powder shaker has a special feature: automatic adjustment of oven temperature. When the oven temperature exceeds 120℃, the film may be baked, so it is necessary to reduce the temperature, so as to ensure the output quality.
6. Design reasons
Sometimes, the printing effect appears white edges or a lot of white dots, excluding all the problems described above, and can not solve the problem, you need to look at the original design draft, whether the product pattern provided by the customer itself has white edges or white dots, but because it is hidden deeper, it is not easy to be found. So this is not the equipment problem of the white ink hot stamping printer itself.
Therefore, in this case, it is necessary to ask the customer whether to retain or change the design drawing, or improve it according to the designer’s suggestions.
In summary, in the case that the DTF printers encounters the shake powder shake is not clean, the above reasons should be investigated first. If it still cannot be solved, it is recommended to seek the help of the manufacturer. I wish all owners with DTF printers smooth printing, good luck!